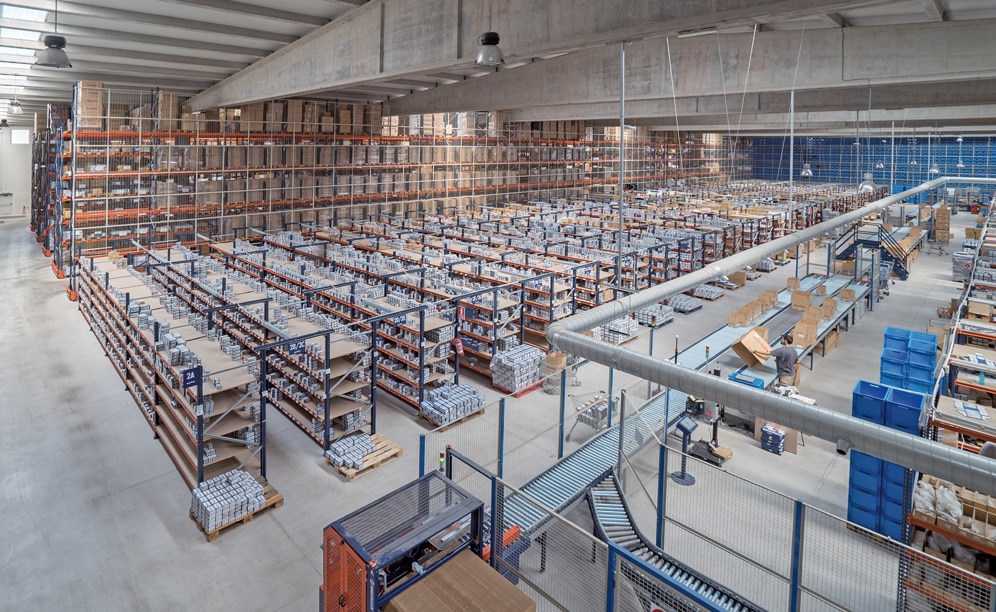
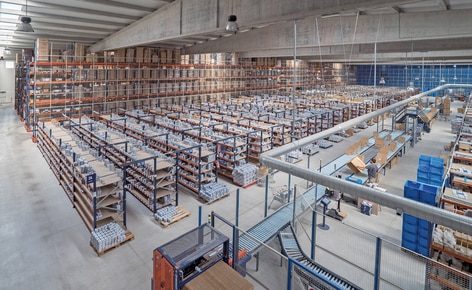
Innovation and agility in the picking of online sales of industrial, hardware, and DIY supplies
The new Cofan logistics center is zoned into different areas and is focused on picking
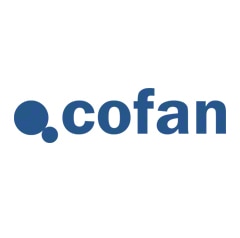
This newly built modern logistics center is zoned into different areas, organizing Cofan’s goods according to its characteristics and level of demand. Mecalux has provided all storage systems within the installation (including an automated miniload warehouse) and a complete circuit of conveyors with P&D stations, box formers, box sealers, scales and classification chutes. This solution allows picking to be carried out swiftly and efficiently.
关于Cofan
Cofan is a company with over 15 years' experience in the development and online sale of industrial supplies, hardware and DIY products. It has three different brands (Cofan, Bricofan and Cofan Home) sold in more than 12 countries.
The business intends to strengthen its growth through innovation and the introduction of technology in all its production processes. Currently, Cofan is a pacesetter in the industrial and automotive sector, as well as a trusted online distribution brand.
Needs of Cofan
The strong growth experienced in recent years compelled Cofan to build a new logistics center that bore in mind both short and medium-term expansion. The company needed to obtain the maximum storage capacity and classify products by SKUs to expedite the preparation and consolidation of orders. Also, it required lower operating costs and to ensure efficient service for users of its e-commerce platform.
They requested the collaboration of Mecalux to find a fitting solution that would adapt to all its prerequisites, allow an increased number of daily dispatches and also improve order delivery times. The project was a challenge because of the diversity of products sizes, weights and different classifications based on ABC turnover criteria, which each required a very in-depth analysis.
The logistics center
The result is this new logistics center, located in the town of Campo de Criptana, 93 miles from Madrid, and very close to the main logistics platforms of the Iberian mainland. It is found in an important transport hub that facilitates optimal distribution of products throughout Spain. The 6.2 acre warehouse is sectored into different areas according to the company's stipulations, which classifies each product family based on its level of demand and dimensions. The predominant operation is picking, with many orders and few prep lines for each of them.
These are the different parts and sectors of the warehouse:
- Manual picking warehouse for consumer goods
- Reserves warehouse
- Reserves warehouse and picking of bulky products
- Automated miniload warehouse
- Sensitive product warehouse
- Automatic box formers
- Conveyor circuit and prep tables
- Consolidation and inspection area
- Order classification area
Picking: the primary function of the logistics center
Because of the characteristics and types of orders, the central part of the warehouse is set aside for consumer products. High accessibility was essential in this area — as well as flexibility — with a variable number of operators depending on the demand and the time slot.
To meet this target, low-rise racking was installed with a limited volume of SKUs. There are reserve pallets of these products on both sides of the racks in the picking and the replenishment area which is carried out during off-peak hours, i.e., when there is less order preparation work.
Running through the center of this area is a circuit of conveyors moving at a speed of 148 ft/min and where six, large capacity roller tables are arranged, on both sides, for the preparation of orders.
Box former
The whole process starts with the formation of boxes. This task is done by four automatic machines (each assigned to a different sized box) located at the beginning of the conveyor circuit.
The warehouse management system (WMS) tells the box formers the quantity and the size of boxes the orders require, taking into account the composition of each wave being prepared. The boxes, identified through allocation and labelling, are progressively sent towards the conveyor circuit to the first prep table, where the product needed for its order is found. The operator reads the label on the package with an RF terminal to determine what material should be inserted.
Manual picking warehouse
Each of the six tables in the prep zone corresponds with a certain rack number. Operators roam the aisles of the racks using carts to pick up the SKUs that the WMS has indicated using the RF terminal.
After this phase, the order is returned to the conveyor belt to be moved to the next station that contains the necessary products. If it is completed, the conveyor automatically routes it to the consolidation and classification area.
Automated miniload warehouse
After this high throughput zone, there are supplementary prep tables attached to the automated miniload warehouse for boxes. In this area, small-sized and rarely consumed products (mainly type B and C) are located.
Consumption of these products fulfills the Pareto Principle or 80/20 rule, i.e., 80% of the SKUs account for only 20% of the warehouse movements.
Sensitive product warehouse
Afterward, the conveyor circuit flows to the pallet racks where the bulky and lower demand products are deposited. Right next door, the sensitive product warehouse constitutes the last stage of the circuit.
Completion
Completed orders are moved to the consolidation area, where the packaging, labeling and issuing of the required shipping documentation take place.
In this area, there are two sets of scales, box sealers and fully automatic labelers given the needs of the company and because of the large number of orders that are produced daily.
Once the finished orders pass through the consolidation area, they are sent towards the five classification chutes located in front of the loading docks. There they are grouped by routes and transport agencies before being dispatched.
Miniload warehouse
In the automated warehouse for boxes, smaller and low turnover products are housed. In this area of the logistics center – where order picking is performed in accordance with the "goods-to-man" principle – put-to-light devices are installed that streamline operations and minimize errors from manual management.
There are two picking stations where operators receive boxes from the warehouse and, just behind them, a table for picking with a capacity for eleven simultaneous waves of orders.
Stacker cranes place containers (Euro-boxes) with the goods on the conveyors, which automatically move them towards the picking stations. Operators extract the products that the system indicates on a screen and deposit them in the corresponding cardboard box on the picking table.
Put-to-light monitors visually guide the operator via three different colors, which tell them where to put each item. The operator taps the display to confirm that they have carried out the action.
The automated warehouse is comprised of three aisles with single-depth racking on both sides. The racks have 19 levels, reaching a height of 28’.
一个单立柱miniload码垛机沿着each aisle that is tasked with managing the inputs and outputs of the goods. These machines operate at a travel speed of 590 ft/min and 328 ft/min when elevated.
The stacker crane is equipped with an extraction system with forks. These forks are inserted under the bottom of the boxes and extract or place them in locations on both sides of the aisle.
At the rear of the aisles, a maintenance area is set up with safety access doors that ensure the well-being of the operators. The stacker cranes are sent there when they require any sort of intervention or repair.
Easy WMS by Mecalux
The automated picking warehouse is managed by the Easy WMS warehouse management system by Mecalux, which is responsible for controlling and coordinating its correct operation.
This powerful system performs various operations, which include the allocation of locations and the storage of boxes according to its turnover, extraction of goods and preparation of orders.
Easy WMS by Mecalux is in constant two-way communication with Cofan's general warehouse WMS and ERP, transferring data and information for maximum picking productivity and throughput.
Different storage systems
The distribution of different storage systems installed in the logistics center fits the variety of products available and takes into account demand and turnover; allowing the speedy preparation of orders.
Consumer and smaller sized product are centrally housed, where 59 picking racks were installed, 8.2’ high and 8.9’ long, consisting of three or five levels with shelves.
The aisles are wide enough, so operators move swiftly and without interference. A RF terminal connected to the WMS of the warehouse permits the identification and classification of the products. Users prepare orders in waves, i.e., several orders at a time, to optimize the route along the locations within the facility.
Around the manual picking area for consumer goods, 25’ high pallet racks were installed. High-volume goods and reserves of high turnover products are stored there on pallets. In addition, picking is directly carried out on the lower levels.
Operators use low-level order pickers since they are adapted to picking in an ergonomic position and can move up two pallets at a time.
An underpass is enabled that cuts across the racking and serves as the emergency exit, in addition to facilitating the flow of goods. The bays on top of the safety passageway are enclosed with mesh to avoid material from falling.
Advantages for Cofan
- Enormous storage capacity:the new 6.2 acre Cofan logistics center is equipped with various storage systems that cater to its wide variety of products, of very different dimensions.
- Efficient order preparation system:的分配ibution of the goods, taking into account their characteristics and demand, allows for the optimization of the movement of operators and maximum throughput of picking.
- Proficient management:the combination of the different software programs implemented in the installation, both management and control, along with the Cofan ERP, get the most out of all resources.
Automated miniload warehouse of Cofan, Spain | |
---|---|
Storage capacity: | 14,334 boxes |
Max. weight per box: | 66 lb |
No. of stacker cranes: | 3 |
Warehouse height: | 28’ |
Storage levels: | 19 |
Picking stations: | 2 |
Ask an expert
Request information or get a quote