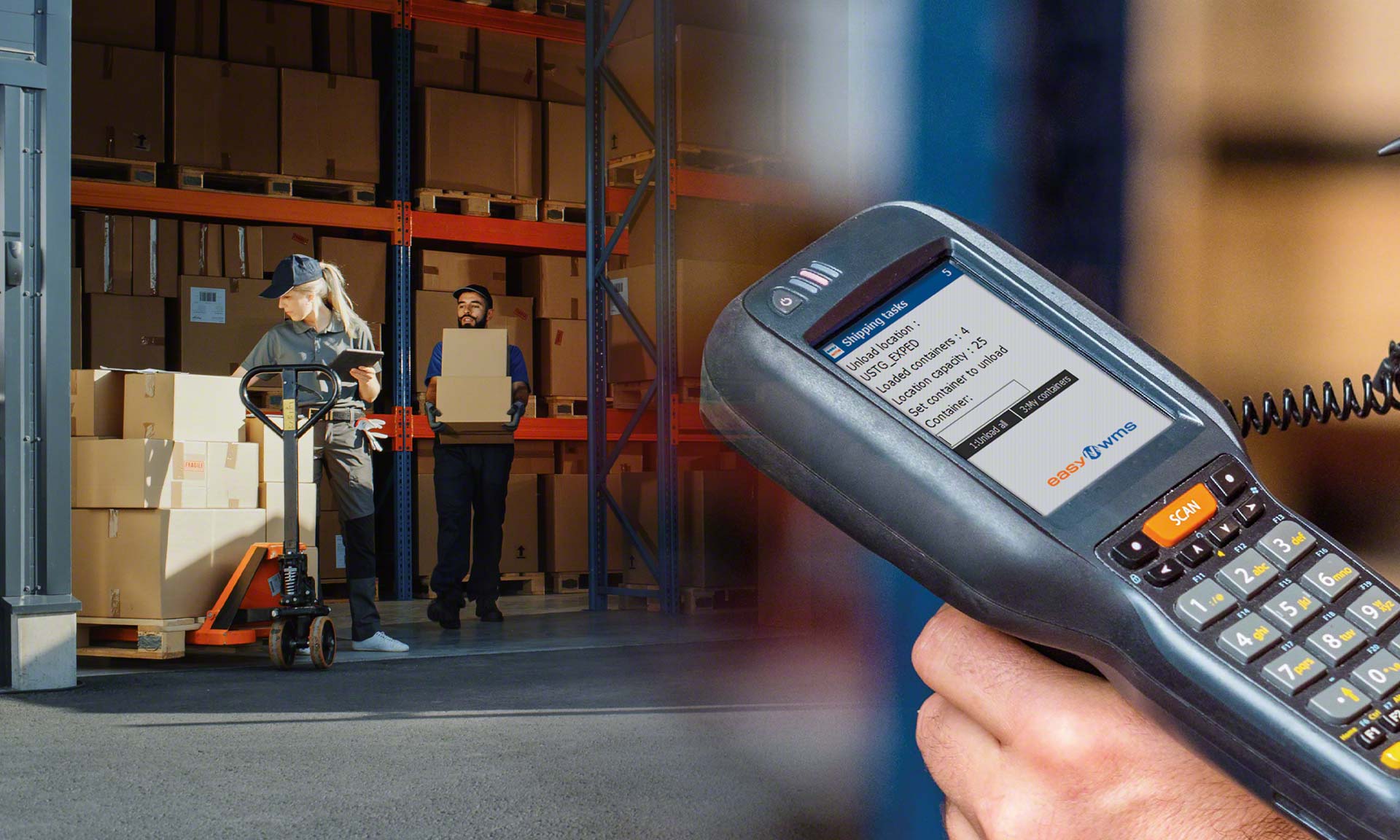
Ecommerce retailer GreenlandMX digitizes its warehouse
GreenlandMX, an e-commerce retailer of motorbike accessories, triples its order numbers with Easy WMS from Mecalux.
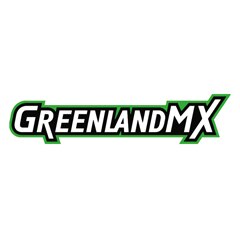
GreenlandMX, an online store for accessories, spare parts, and gear for off-road motorcycles, has installed Mecalux's Easy WMS software in its warehouse. The WMS has increased productivity, tripling the number of orders prepared every day.
GreenlandMX: specialists in off-road motorbikes
GreenlandMX is an online store for off-road motorbikes and accessories. Based inValdorros, Spain, the company has been selling products via its website for over 15 years, making it a benchmark for online sales in its sector.
- 总部:Valdorros
- Founded in:2004
- No. of employees:30+
挑战
|
SOLUTIONS
|
BENEFITS
|
---|
GreenlandMX is an online store specializing in accessories, spare parts, and gear for off-road motorcycles. The business has marketed its products online for over 10 years, becoming a leader in its sector.
For its business and online store to run optimally, GreenlandMX requiresflawless organization of its logistics processesto enable same-day dispatch of all orders placed by customers through the website. “Our modern warehouse, which is about64,600 ft², storesmore than 23,000 SKUs. This storage capacity and the proper distribution of the goods enables us to deliver orders in record time and at the best possible price,” says Javier Solas, Manager of GreenlandMX.
The company also set up a physical store in its facility. Open to the public, customers can shop for items they need as well as pick up orders they have purchased online.
To simultaneously manage stock and orders in the warehouse and the store,GreenlandMX opted to digitize its logistics operations withEasy WMS software from Mecaluxand theWMS for EcommerceandMulti Carrier Shipping Softwaremodules. “We came to realize that managing our facility manually with the SAP ERP system was inefficient. In installing Easy WMS, our goal was to optimize location utilization, minimize operator travel in the warehouse, and maintain tighter inventory control,” says Solas.
GreenlandMX决定安装容易WMS当number of daily orders started to climb. “We needed to digitize our facility because we could no longer manage orders manually. We were wasting a lot of time locating products for each order and controlling stock. Managing a warehouse manually when you’re preparing 50 or 60 orders a day is viable, but when you go beyond that, you have to digitize,” says Solas.
The GreenlandMX facility is equipped withracks that occupy practically all available floor space. They are designed to store individual products such as spare motorbike parts and accessories. The warehouse also has a large receiving and dispatch area that acts as a buffer. There, the goods the company receives from suppliers are deposited on the floor until they are assigned a location or even re-dispatched.
In the GreenlandMX facility, theMecalux software coordinatescross-docking, whereby orders are distributed directly without being stored previously. “Easy WMS is configured to manage cross-docking, which we do in the receiving area. For instance, when 100 units of a product arrive, the WMS might tell us to leave 25 units in cross-docking because they have to be shipped that same day. It’s a functionality we use quite often and that saves a lot of time,” says Solas. The software also controls and optimizes another key operation in the GreenlandMX warehouse: “We receive returns for about 3% of our total orders.Easy WMS organizes returns as if they were just another good received,” says Solas.
WMS for Ecommerce: optimization of online orders
The main operation in the GreenlandMX facility is order picking. With the help of Easy WMS, the company hasoptimized and enhanced the work of its operators, tripling the number of orders prepared every day.
“Before implementing the Mecalux software, we prepared around 170 orders a day. Now, every day, we dispatch 500 orders that are distributed throughout Europe,” says Solas.
The company, which had been using the SAP ERP system to prepare orders, chose to install the WMS for Ecommerce module from Easy WMS to drive this operation. With its highly intuitive interface, this program hassimplified workflows, increasing productivity.
WMS for Ecommerce organizes order picking starting in the receiving area. There, operators identify the products that arrive at the warehouse. The software then decides what to do with each of them: store them or ship them the same day. To prepare orders, the program sorts items based on whether they are part of asingle- or multi-unitorder.
“We’ve seen an improvement in our facility since implementing Mecalux’s WMS for Ecommerce module. The system has been customized to adapt to our needs, and it facilitates order picking tremendously,” says Solas.
Using a cart with eight trays — each corresponding to an order — the operators walk through the warehouse locating the items they need to put together each order. Following instructions from the software, they can prepare up to eight orders simultaneously.
Transferring data and information in real time,the ERP system and WMS for Ecommerce module communicate with each otherto ensure the efficient operation and management of the facility and get the most out of all logistics processes.
Goods storage
“Easy WMS assigns a location to each product taking into account its turnover rate,” says Solas. As they are small, the motorbike parts and accessories are stored in small plastic or cardboard boxes that are then placed on the racks. Rather than recording each box in the system separately, Mecalux’s Easy WMS controls the rack locations and the goods they contain. Each product is assigned a location on the racks and labeled with a code. A location can hold more items or fewer items depending on its size or on the quantity required to perform picking. One advantage of the software is the ease with which GreenlandMX can modify the products assigned to each location.
To streamline the work of the operators,Easy WMS can assign items locations on the go. For example, if operators need to store a new product, they can assign it a location using theirRF scanner.
也容易WMS管理补充, showing the operators how many goods to replenish and which positions to deposit them in. This operation is typically carried out in the morning, although it can also take place during off-peak hours during the day, i.e., when there is a lull in picking.Correct organization of replenishment avoidsstockouts, which prevent operators from filling orders on time.
The physical store open to the public in the GreenlandMX facility sees quite a few customers. When the store clerks need more stock, they can go directly to the warehouse to pick it without having to wait to receive it. The software strictly controls the movements of the goods to avoid inventory imbalances.
Multi Carrier Shipping Software: dispatch organization
“The Multi Carrier Shipping Software module allows us to integrate our entire dispatch management process with the transportation agencies and to minimize our error rate. The minute we close an order,Easy WMS generates the labels, the packing list, and all the documentationthe carrier needs to distribute the shipments,” says Solas.
Multi Carrier Shipping Software is designed to oversee all packing, labeling, and shipping processes. The software sends precise instructions to operators on how to pack the orders (e.g., it tells them whether to place all items in a single package or in several ones). The next step is order labeling.Multicarrier Shipping Software knows in advance which agency will distribute each orderand prints a personalized label for each parcel. The label includes, among other details, the tracking number that customers can use to monitor their orders in real time. In the GreenlandMX facility, the module connects with the transportation agencies SEUR, Correos Express, DPD, DHL, and UPS.
Once the labeling process is finished, the packages are organized in the dispatch area. When the carriers arrive, they merely have to pick up the parcels and load them onto the truck. Thanks to the software, the carriers have all the information they need, such as the orders to collect, the number of packages, and the destination.
Forward-looking logistics
“Our focus is on continuing to grow as we’ve been doing since 2004. We also want to expand the number of countries where our orders are shipped. In terms of sales, 2020 and 2021 have been very good years, as a result of the boom in online shopping,” says Solas.
The Mecalux warehouse management software hasboosted productivity in GreenlandMX’s facility, tripling the number of orders prepared on a daily basis.
“Easy WMS manages the warehouse comprehensively: it controls stock and implements an advanced product location and order picking strategy. All processes in our facility are optimized,” says Solas.
Easy WMS has been adapted to our needs and organizes all operations in our facility with maximum efficiency. Before implementing the Mecalux software, we prepared around 170 orders a day. Now, every day, we dispatch 500 orders that are distributed throughout Europe.
Ask an expert
informa的请求tion or get a quote