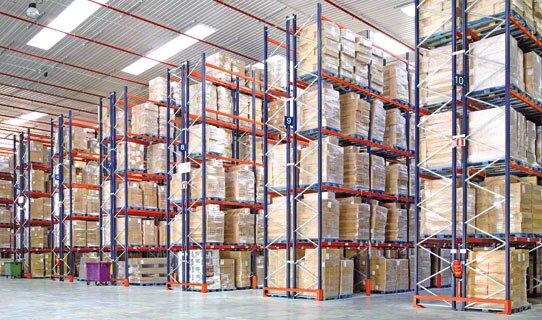
Logistics remodeling of Cofan Center to reduce operating costs
The center, designed and set up by Mecalux, has provided Cofan with streamlined work flows, making one-day delivery services to customers a reality.
Video transcription
Ciudad Real in Spain, is home to the Cofan logistics center, a company with over 15 years of experience in the industrial supply, hardware and DIY sector.
The center, designed and set up by Mecalux, has provided Cofan with streamlined work flows, making one-day delivery services to customers a reality.
Venancio Alberca (General Director at Cofan)
When we decided to implement a logistics system, like the one we have here at Cofan, there were a number of questions we knew had to be answered about what we really needed. One had to do with the diverse products we carry, and their various sizes and features. Another was about product turnovers, ranging from items with a high turnover to others with a low one. From this initial plan, Mecalux began to shape the project, developing it based on product logistics. The result is evident today in our installations: modern facilities where we have the low turnover products located in the AS/RS miniload for boxes, average turnover products in the picking area and consumer goods in another area set up to prepare orders with automatic order pickers.
The warehouse is divided into five main areas, linked by a conveyor circuit that runs through the warehouse from front to back.
At the beginning of the circuit, four box forming machines set up boxes and place them on the conveyors. These mechanical devices stock the picking area with four types of boxes that are combined, depending on the product volume.
Once assembled, the boxes flow along the conveyor circuit into the central picking area. In this area, there are six large capacity roller tables enabled for zone based order prep. Operators on both sides of the conveyor belts collect boxes and place the product allocated to each order inside.
拣选货架是d的补充one with product from the selective pallet racking situated on both sides of this picking area.
The boxes automatically flow past the various tables that contain the product for each order. Operators push hand carts around the aisles collecting the SKUs the WMS lists on the handheld RF devices.
If the order is completed, the conveyor automatically moves it to the end of the circuit; if it is not complete, the boxes move to the next picking station.
Venancio Alberca (General Director at Cofan)
Warehouse personnel now work in a much more user-friendly manner. They don't have to travel long distances to complete a package because it is the package that moves to them, until it is finished at the end of the line. Then, it is automatically closed, sealed and dispatched via the designated transport agency.
Beside the central picking zone is the AS/RS miniload for boxes, which supplies small-sized and low demand products.
This fully automated miniload system has three aisles, each with a stacker crane that moves product to and from 19 different storage levels. This warehouse has an overall capacity of almost 15,000 boxes.
The Mecalux Galileo software is responsible for controlling the movements the stacker cranes carry out.
The AS/RS miniload system has a closed circuit that transports boxes to the various picking stations.
Following management system’s orders, operators collect products and introduce them into the corresponding boxes.
After completing the order, operators validate the box so it can continue on its way through the rest of the circuit.
Beyond the AS/RS miniload for boxes, continuing along the same conveyor circuit, boxes arrive at the sensitive materials area, which is separated from the remainder of the warehouse by fire resistant walls due to the flammable nature of these products.
Leaving the sensitive products warehouse behind, the boxes travel a short distance to the consolidation zone, which controls and validates the weight of the goods. If it is not suitable, the box is rejected by the system and diverted to an aisle to be adjusted.
Finally, the goods coming from the distinct parts of the warehouse reach the sorting area, where the order is sealed and labeled for distribution.
The end of the circuit is equipped with a sorter connected to the warehouse management system, which distributes the goods into the five dynamic channels for their subsequent dispatch.
The Cofan center is a logistics icon among companies working with multiple SKUs.
Logistics remodeling of the center has enabled the company to reduce operating costs and achieve its goal of offering a one-day delivery service to its customers.